Contractors involved in the construction of an A$80 million retail centre in the heart of the Sydney metropolitan area have managed to minimise the number of workers on site by incorporating LYSAGHT BONDEK® structural steel formwork.
Reed Constructions project manager, Jim Mitchell and Superior Formwork project manager, Rade Dundovic, estimate that the use of LYSAGHT BONDEK® has resulted in less workers being required to build the Auburn Power Centre than would have been the case if conventional formwork had been used.
Due for completion in September 2006, the three level Auburn Power Centre complex is located on one of Sydney's busiest roads and will house high profile tenants from the bulky goods retail segments.
The complex was designed by the Melbourne office of architecture practice, The Buchan Group. Multidisciplinary consultants Grogan Richards provided structural, civil and traffic engineering services.
Grogan Richards project engineer, Michael Webb, explained the background to the building design.
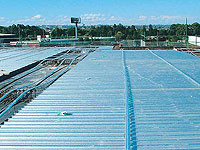
"On the structural side we designed the formwork component with LYSAGHT BONDEK® in mind, but we didn't specify that," he said "We left that decision up to the builder."
"When it went out to tender Reed Constructions and several other tenderers responded with a recommendation to base the steel formwork on the LYSAGHT BONDEK® system. "There were reservations on the architects' side from an aesthetics point of view because this is a retail centre, but then the option of using LYSAGHT BONDEK® with a white pre-painted underside for the carpark and external areas was put forward."
"We were all looking to save money and it soon became obvious that we could do so with LYSAGHT BONDEK®. Reed Constructions were able to offer up a saving because of the LYSAGHT BONDEK® and the prepainted finish to the structural steel formwork also provides extra brightness and enhances security."
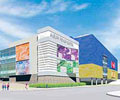
"The client is extremely happy with that aspect and in fact he is extremely happy with the LYSAGHT BONDEK® in general, to the extent that he is now asking for it on many of his other projects."
Michael Webb said Reed Constructions had specified 1.0mm LYSAGHT BONDEK® with a prepainted white underside for the carpark and 0.75mm galvanised LYSAGHT BONDEK® for other areas throughout the site.
The material was delivered to site in lengths up to 8.0 metres, with the majority pre-cut for the building's 6.15 metre spans between band beams.
"At our first site meeting Reed Constructions demonstrated that the deflections even over long spans were negligible. Equally importantly there were no discernable permanent deformations to the underside of the LYSAGHT BONDEK®. In fact it looked very good. It's one of the best looking steel decking jobs I've seen."
Reed Constructions project manager Jim Mitchell had looked at all possibilities for the building's formwork.
"In my initial discussions with Rade Dundovic from Superior Formwork we talked about the number of men needed to lay out the 50,000 square metres of formwork in a limited time," Jim Mitchell said.
"When we decided to go with LYSAGHT BONDEK® instead of plywood that number was significantly reduced. We hadn't been involved with LYSAGHT BONDEK® before, so we valued Superior Formwork's opinion. They convinced us that its advantages such as labour savings could be helpful, particularly on a job like this where the project is large and the whole design and construction process has been fast tracked."
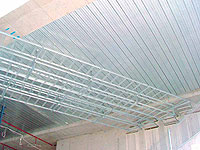
"The LYSAGHT BONDEK® formwork is lightweight compared to plywood and it is quicker to put down. This makes it extremely competitive with conventional formwork and resulted in a significant saving because of the quantity involved. On the basis of their investigations, Reed Constructions decided to specify LYSAGHT BONDEK® formwork and then began to program building activities around the time savings which Superior Formwork indicated."
Since then they have been able to increase the pace of construction to stay ahead of their own ambitious schedule.
"LYSAGHT BONDEK® is ideal for a job like this," Rade Dundovic from Superior formwork said. "This is one of the largest jobs our company has tackled, but we will be finished at least a month and probably eight weeks ahead of when we would have if conventional formwork had been used. The clean up process with LYSAGHT BONDEK® is also good," Jim Mitchell said. "Once the formworkers take out the support beams and back props there is nothing else to remove. The site just needs a sweep."
"You save money on the clean up costs and I've also had people walking onto the job commenting on how clean the construction site is," he said.
"Once it is clean you make an extra effort to keep it that way. The initial strip leaves it a lot cleaner than you would get with plywood formwork."
Rade Dundovic agrees. "For a start you don't have a million nails to pick up," he said. "On this sort of project you can't beat it, but the main advantages with LYSAGHT BONDEK® here have been the combination of speed and lower costs. You couldn't use conventional formwork to match the speed of what we have achieved here, no matter how many workers you employed."
Jim Mitchell has also found that the clean strip out, leaving only back props, allows service trades to follow on sooner than would be the case with conventional formwork.
"In some parts of this job the tradesmen installing services are catching up to the formwork strip out," he said.
"The speed we are making on this project is such that at one end we are putting up ceilings and partition walls and at the other we are still pouring concrete. What you see here represents seven months work. When you look at the progress of other large jobs around Sydney, we have achieved a lot."
"The advantage is that when a project is going as well as this the workforce see the progress and they want to keep it going. There is pride involved, people aren't just turning up to collect a wage, so there are all sorts of benefits to be had from using time saving materials such as LYSAGHT BONDEK®."
LYSAGHT BONDEK® decking is the original steel formwork system that revolutionised concrete construction. It is made from DECKFORM® zinc coated high tensile steel which was developed by BlueScope Steel specifically for the steel decking market. It delivers excellent durability and is backed by a BlueScope Steel warranty and nationwide technical support.