Newcastle's coal loader project was a tailor made opportunity for Redispan modular conveyor systems, thanks to the restricted site access and the resultant need for off-site pre-assembly.
The ability to supply fully prefabricated sections to the site was crucial on this project, as was the relatively light weight of the sections and the subsequent lack of heavy lifting. For the Down Group at Campbelltown, south west of Sydney, the project was also a showcase for Redispan's many other attractions. But perhaps more than anything, the project highlighted the way in which smart marketing of a good idea can find a much broader market than that for which the product was originally designed.
When the system was first brought to market a decade ago, it was specifically designed to meet a need for water containment during wash down. The prime requirement was for a continuous gallery system that could be fully sealed, and initially this was the principal design objective.
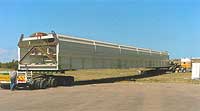
Redispan comprises a structural side cladding, a continuous structure to facilitate wash down and assist in load distribution, and a trestle system that takes full advantage of the continuous spans. From the outset, there was a clear market because of the environmental and OH&S benefits of the system. Naturally, the system had to be cost effective to meet these markets, and this became a major attraction in its own right.
According to Down Group General Manager Peter Lee, it soon became apparent that the elegant, economical, prefabricated system had much wider appeal. Environmentally, the fully sealed system offers both dust reduction and noise attenuation in addition to its washdown benefits. It also has a small footprint for minimal site disturbance, plus an undeniably tidy appearance. The opportunity for off-site assembly, though, has proved to be a decisive factor on jobs such as the coal loader.
The Port Waratah installation is the largest single job yet for Redispan, with a total installed value of A$12 million. It represents the growing popularity of the system in a variety of industrial and mining applications. Although limited site access was a key consideration at the coal loader, other projects have featured Redispan for its other attributes.
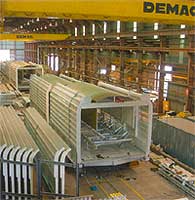
Structurally, Redispan is a steel-intensive composite structure that was developed specifically with customers in mind, so cost effectiveness was always an overriding consideration. Key elements of the design are its structural steel side cladding, steel or concrete floor and lightweight curved steel roofing, all combined into a fully sealed unit.
Computer aided design (CAD) ensures that the system can readily be customised to suit each specific application. With all drawings for a quoted job stored on the CAD system, production can start immediately upon receipt of a confirmed order. This can lead to significant time savings, as gallery module production can proceed while other design details such as trestle type and location are finalised.
Individual modules measure up to 12 metres, with widths between two and six metres, and modules can be joined to achieve spans up to 48 metres. Customised internal layouts may include one or two conveyors and single, double or triple walkways, and the design includes an overhead conveyor support structure. Down Group offers full factory fit-out of all services and conveyor idlers if required.
Curved surfaces and round tubular sections are used to reduce dust accumulation, and the enclosed galleries are less susceptible to wind effect than conventional open galleries. The roof is made of curved LYSAGHT CUSTOM BLUE ORB® steel, and the cylindrical trestles can be arranged in an A-frame or as single legs to minimise the ground area required.
Down Group describes its system as "arguably world's best practice conveyor gallery system", and the marketing highlights its full range of attractions. Having developed its product to meet one specific market, Down Group is now geared up to offer Redispan as a market driven solution in a wide range of applications.